Seramik elyaf kompozit

Fotoğraf: MT Aerospace , Augsburg
Seramik elyaf kompozit malzemeler , kompozit malzemeler veya teknik seramikler grubu içindeki bir malzeme sınıfıdır . Uzun lifler arasına gömülü, seramik liflerle güçlendirilen ve böylece lifle güçlendirilmiş seramikler , kompozit seramikler veya basitçe fiber seramikler haline gelen normal seramiklerden oluşan bir matris ile karakterize edilirler . Alman uzman literatüründe, malzeme sınıfı İngilizce'de genellikle Seramik Matris Kompozitleri olarak anılır ve CMC olarak kısaltılır. Matris ve lifler prensip olarak bilinen tüm seramik malzemelerden oluşabilir ve karbon da bu bağlamda bir seramik malzeme olarak işlem görür.
Makale, şu anda endüstriyel olarak temin edilebilen kompozit seramikleri en önemli üretim süreçleri, temel özellikleri ve bu nispeten genç malzeme grubunun bazı geliştirme ve başarılı uygulama örnekleri ile açıklamaktadır.
Giriş
Kompozit seramiğin Geliştirilmesi ve Uygulanmasında şu anda öncelikle karbon ve sözde silikon karbür elyaflar ve daha az ölçüde alümina elyafları (Al 2 O 3 ) veya karışık alümina ve silika kristalleri (SiO 2 ), sözde mullit gelmektedir. oluşur. Halihazırda teknik uygulamalarda kullanılan ana matris malzemeleri alüminyum oksit, mulit, karbon ve silisyum karbürdür ( Kaynak : W. Krenkel, 2003).
Bu seramikleri geliştirme motivasyonu , alüminyum oksit , silisyum karbür, alüminyum nitrür , silisyum nitrür veya zirkonyum (IV) oksit gibi geleneksel teknik seramikler kullanılırken ortaya çıkan sorunlardan kaynaklandı : tüm bu malzemeler mekanik veya termomekanik yükler altında kolayca kırılır, çünkü kendileridir Yüzeydeki küçük üretim hataları veya çizikler bir çatlağın başlangıç noktası olabilir. Metallerin (anahtar kelime: süneklik ) aksine, ancak cama benzer şekilde , çatlakların yayılmasına karşı çok az direnç vardır. Birçok uygulamayı zor veya imkansız kılan kırılgan bir kırılma davranışı ile karakterizedir. Seramik içine yabancı partiküller, monokristal kısa lifler (sözde bıyık ) veya diskler ( trombositler ) yerleştirerek bu özelliği iyileştirmeye yönelik gelişmeler , çatlama direncini yalnızca sınırlı bir ölçüde iyileştirebilmiştir , ancak bazılarında kullanılmıştır. seramik kesme aletleri . Sadece seramiği güçlendirmek için uzun liflerin kullanılması bu çatlak direncini büyük ölçüde artırabildi ve daha fazla süneklik , kırılma tokluğu ve termal şok direnci gibi yeni uygulama alanlarının açılabildiği ve açılabildiği gelişmiş özelliklere yol açtı.
Bu şekilde üretilen kompozit seramikler genellikle "elyaf tipi / matris tipi" şeklinde kısaltılır. Örneğin, "C / C", karbon fiber takviyeli karbon anlamına gelir veya "C / SiC", karbon fiber takviyeli silisyum karbür anlamına gelir. Üretim süreci bu kısaltmaya dahil edilecekse, genellikle (ve ayrıca aşağıdaki makalede) “üretim süreci-elyaf tipi / matris tipi” olarak kısaltılır. Örneğin, sıvı polimer infiltrasyon işlemi (aşağıya bakınız) kullanılarak üretilen karbon fiber takviyeli bir silisyum karbür basitçe "LPI-C / SiC" olarak adlandırılır.
Şu anda endüstriyel olarak temin edilebilen en önemli elyaf takviyeli seramikler C / C, C / SiC, SiC / SiC ve Al 2 O 3 / Al 2 O 3'tür . Aşağıda daha ayrıntılı olarak sunulan özelliklerde geleneksel teknik seramiklerden farklılık gösterirler:
- yüzde bire kadar kırılmada daha yüksek uzama
- önemli ölçüde daha yüksek çatlak direnci
- aşırı termal şok direnci
- daha iyi dinamik esneklik
- elyaf yönelimlerine dayalı anizotropik özellikler
Tarih
CMC'leri sıvı, gazlı veya katı başlangıç malzemeleri kullanarak işlemek için birkaç yaklaşım mevcuttur. Kimyasal gaz fazı sızma (CVI) tekniği, CMC'lerin gelişimini destekledi. CVI tekniği, 1960'lardan beri Kimyasal Buhar Biriktirme (CVD) teknolojisinin bir uzantısı olarak incelenmiştir. CVD, gaz halindeki öncülerden ısıtılmış bir substrat üzerinde bir katının biriktirilmesini içerir. Uzun yıllardır aşınmaya dayanıklı kaplamalar, nükleer yakıt kaplamaları, elektronik devreler için ince filmler, seramik elyaflar vb. Yapmak için kullanılmıştır. CVD tekniği, nispeten büyük miktarlarda matris malzemesini elyaflı preformlara emprenye etmek için kullanıldığında, CVI olarak adlandırılır. CVI ilk olarak 1000–2000 ° C'de metanın pirolizi ile karbon-karbon kompozitleri üretmek için kullanıldı. Karbon-karbon (C / C) kompozitleri birçok avantajlı özelliğe sahiptir (örneğin, düşük yoğunluk ve yüksek sıcaklıklarda iyi mekanik özellikler gibi). Bununla birlikte, 1973 civarında, C / C kompozit uygulamalarının, 450 ° C'nin üzerindeki sıcaklıklarda zayıf oksidasyon direnci nedeniyle sınırlı olacağı ortaya çıktı. SiC matris kompozitleri, oksidatif ortamda yüksek sıcaklıklarda uzun ömür için yukarıda bahsedilen C / C kompozit eksikliğini gidermek için bir çözüm olarak görülmüştür. Fiber takviyeli CMC'ler, C / C kompozitlerinin ve CVI üretim teknolojisinin gelişimini takip etti. CVI SiC / SiC kompozit geliştirme, 1980'lerde SEP (şimdi SNECMA ), Amercorm , Refractory Composites ve diğerleri havacılık, savunma ve diğer uygulamalar için CMC bileşenleri üretmek için ekipman ve süreçler eklemeye başladığında başladı. SNECMA, bu teknolojinin ön saflarında yer aldı ve türbin motorlarında tatmin edici performansa sahip çeşitli CVI-SiC / SiC bileşenlerini gösterdi. Bir dizi CVI-SiC / SiC bileşeninin türbin motorlarında ve diğer bileşenlerde başarılı olduğu kanıtlanmıştır. CVI-SiC matris kompozitlerinin fizibilitesi 1977'de araştırıldı ve 1978'de bağımsız olarak onaylandı. SiC fiberlerle güçlendirilmiş CVI SiC matris kompozitler 1980'lerin sonlarından beri üretilmektedir. Mevcut CVI SiC / SiC kompozitleri, yüksek sıcaklıklar gibi aşırı koşullar altında mükemmel performansa sahiptir. Bu arada, eriyik infiltrasyonu (MI), polimer infiltrasyonu ve piroliz (PIP) gibi alternatif üretim prosesleri ve CVI ve diğer metotları birleştiren hibrit yaklaşımlar geliştirilmiştir. Son 30 yılda CMC gelişmelerinde muazzam ilerlemeler oldu.
Genel olarak imalat
Elyaf takviyeli seramikten yapılan bileşenlerin üretimi genellikle üç adımda gerçekleşir:
- Elyafların istenilen komponent şeklinde dosyalanması ve sabitlenmesi
- Elyaflar arasına seramik matris malzemesinin tanıtılması
- Bitirme ve gerekirse kaplamaların uygulanması gibi diğer işlem sonrası adımlar
İlk ve son adım, tüm elyaf takviyeli seramik türleri için hemen hemen aynıdır:
İlk aşamada, elyaflar (teknik olarak fitiller olarak da adlandırılır ), elyaf takviyeli plastik üretimine benzer şekilde çeşitli teknikler kullanılarak yatırılır ve sabitlenir: elyaf kumaşların serilmesi , sarma, örgü veya örgü elyafları buna örnektir. Üçüncü ve son aşamada, elmas aletlerle tüm seramiklerde olduğu gibi , geleneksel taşlama , delme , lepleme veya frezeleme işleme teknikleri yaygındır. Elyaf takviyeli seramiğin kendine has özellikleri nedeniyle su jeti ve lazerle işleme teknikleri de sorunsuz bir şekilde mümkündür.
İkinci adım şu anda prensipte seramik matrisi elyaflar arasına getirmek için beş farklı yöntemi biliyor:
- Seramiklerin sıcak gaz karışımından biriktirilmesi
- Tarafından Üretimi piroliz Si ve C atomu içeren bir polimer
- Kimyasal reaksiyon yoluyla üretim
- Göre üretim sinterleme düşük sıcaklıklarda (1000 1200 ° C)
- Tarafından Üretimi elektroforezi seramik tozu ile
Beşinci yöntem henüz endüstriyel kullanımda değildir. Bahsedilen tüm süreçler için, işlemle ilgili ayrıntılarda ve kombinasyonlarda farklılık gösteren alt varyantlar da vardır. Kitaplarda, uzmanlık dergilerinde ve kongre literatüründe bulunabilir. Aşağıda yalnızca basitleştirilmiş biçimde açıklanmıştır.
İlk üç işlem neredeyse yalnızca oksit olmayanların üretimi için, dördüncüsü ise oksit kompozit seramiklerin üretimi için kullanılır.
Tüm yöntemlerin ortak noktası, aşağıda açıklandığı gibi imalat işleminin gözenekli bir malzemeye yol açmasıdır.
Seramik elyaflarla ilgili notlar
Seramik lifler arasında , yalnızca lifler lif takviyeli seramikle ilişkili değildir, anlaşılır ki, gerçek Teknik Seramikler gibi , bir polikristalin , aynı zamanda , atomların amorf bir düzenlemesine sahip olanları da içerir. Kompozit seramiklerin imalatındaki yüksek sıcaklık nedeniyle, sadece organik değil, aynı zamanda inorganik metal ve cam elyafların kullanımı da hariç tutulmuştur. Yalnızca kristalin alüminyum oksit , mulit (alüminyum oksit ve silikon oksitin karışık kristalleri), büyük ölçüde kristal silikon karbür ve zirkonyum oksitten yapılmış yüksek sıcaklıkta kararlı seramik elyaflar , grafitik lamel düzlemleri elyaflar ve yapılan amorf elyaflar yönünde karbon elyaflar uygulamalarda silisyum karbür kullanılmaktadır. Bu "seramik" liflerin tümü,% 2'nin üzerinde bir uzayabilirlik ile karakterize edilir; bu, bazı durumlarda normal seramiklerin uzayabilirliğinden önemli ölçüde daha yüksektir (yaklaşık% 0,05 ila 0,10). Bunun nedeni, üreticiye bağlı olarak, elyafların çeşitli katkı maddeleri (örneğin oksijen, titanyum, alüminyum, seramik elyafına bakınız ) içermesidir; bunlar olmadan, amorf SiC elyafları, hiçbir zaman% 2'lik bir uzayabilirliğe ve bir gerilmeye sahip değildir. 3000 MPa'nın üzerinde bir güç elde edilebilir. Bu özelliklerle, lifler iki ve üç boyutlu lif yapıları da dokunabilir (şekle bakın). İşleme sırasında, örneğin dokuma sırasında, liflerin yüksek gerilme yüklerine ve küçük bükülme yarıçaplarına dayanması gerekir.
Detaylı üretim
Matrisin bir gaz karışımından biriktirilmesi
Bu işlem, belirli bir gaz veya gaz karışımının malzemeyi ısıtılmış yüzeylere bıraktığı kaplama işlemlerinden türetilmiştir. CVD süreci denir ; CVD, Kimyasal Buhar Biriktirme'nin kısaltmasıdır .
Bu işlem, bir bileşen şeklinde sabitlenmiş bir fiber yapıya uygulandığında, kaplama malzemesi de bileşen içindeki fiber yüzeyler üzerinde biriktirilir. Bu nedenle, bu yöntem aynı zamanda sırasıyla kimyasal buhar infiltrasyonu (engl. Kimyasal buhar infiltrasyonu veya CVI yöntemi ) olarak da bilinir .
Bunun bir örneği, C / C üretimi için bir işlemdir: bir C fiber yapısı, belirli bir basınç altında (genellikle 100 hPa'nın altında) ve sıcaklık koşullarında (genellikle 1000 ° C'nin üzerinde), bir argon ve metan (CH 4 ) karışımı ile üretilir. ) ya da propan (Cı- 3 'H 8 ). Gaz karışımından, karbon fiberlerin üzerinde ve arasında biriktirilir.
Diğer bir örnek, silisyum karbür biriktirilmesidir. Bir şekilde, hidrojen bir gaz karışımı, katalizör ve metil trikloro silan (MTS, kimyasal formül CH 3 trietilamonyum 3 de), bir rol oynadığı üretiminde silikonlar , genel olarak bu amaçla kullanılır . MTS molekülünün karbon ve silikon atomları 800 ° C'nin üzerindeki herhangi bir yüzeyde silisyum karbür oluşturur, diğer H ve Cl atomları hidrojenle birlikte HCl gazı olarak prosesi terk eder.
Çökeltme sırasında, gaz giriş açıklıkları aşırı büyüdüğünde kaçınılmaz olarak kapalı gözenekler oluşturulur.
C ve Si içeren polimerlerin pirolizi ile matris üretimi
Hidrokarbonlardan yapılan uygun polimerler, hacim küçülmesi ve gaz çıkışı ile piroliz sırasında karbon oluşturur. Bazı karbon atomlarının silikon atomları ile değiştirildiği polimerler, örneğin karbosilanlar , benzer şekilde piroliz sırasında, hacim küçülme ve gaz çıkışı ile benzer şekilde amorf ve çoğunlukla karbon bakımından zenginleştirilmiş bir silisyum karbür oluşturur.
Lifler, lifli kumaşlar veya lifli kumaş yığınları ve ayrıca üç boyutlu lif yapıları bu polimerlerle ıslatılabilir veya süzülebilir. Sonraki sertleştirme ve piroliz, yapıyı ilk aşamada sabitler. Hacim daralması nedeniyle, matris bu aşamada hala yüksek gözenekliliğe sahiptir ve bu çoğu uygulama için kabul edilebilir değildir. Gözenekliliği azaltmak için , yapısal bileşeni tamamlamak için genellikle beş ila sekiz ardışık emprenye , sertleştirme ve piroliz döngüsü gereklidir.
Süreç çoğunlukla LPI işlemi olarak kısaltılan Sıvı Polimer Sızdırma ve bazen de PIP işlemi olarak kısaltılan Polimer Sızma ve Piroliz olarak adlandırılır .
Burada da, piroliz sırasında her bir polimer hacim olarak küçüldüğünden artık gözeneklilik vardır. Gözeneklilik, her sızma ve piroliz döngüsü ile azaltılır.
Kimyasal reaksiyon yoluyla matris üretimi
Bu süreçte, başka bir madde ile kimyasal reaksiyona girerek istenen seramik matrise dönüştürülen elyaflar arasında zaten bir malzeme mevcuttur. Geleneksel seramiklerin üretimi de bu tür reaksiyonları kullanır: Reaksiyona bağlı silikon nitrür (RBSN), silikon tozunun nitrojen ile reaksiyonu ile üretilir ve gözenekli karbon silikon ile dönüştürülerek silikon içeren silisyum karbür , sözde SiSiC oluşturulur .
Bu işlemle elyaf takviyeli seramiklerin üretimine bir örnek, yönlendirilmiş eriyik infiltrasyonudur: elyaflar arasındaki erimiş alüminyum, alüminyum oksit matrisine oksijen eklenmesiyle oksitlenir. Eriyikteki alaşım bileşenleri, alüminyum oksit bariyerlerinin oluşumu ile sürekli oksidasyonun kesintiye uğramasını önler. Bitmiş malzeme hala reaksiyona girmemiş alüminyumun kalıntı bileşenlerini içerir.
Seramik fren disklerinin imalatında endüstriyel olarak tanıtılan bir başka örnek, gözenekli bir C / C malzemesinin matris karbonunun sıvı silikon ile dönüştürülmesidir. Vakum altında ve silikonun erime sıcaklığının üzerinde (1410 ° C) kontrollü proses yönetimi ile, matris karbon esasen silikon karbür oluşturmak için reaksiyona girer ve lifler neredeyse hiç etkilenmeden kalır ve böylece güçlendirme işlevlerini yerine getirebilir. Bu işlem genellikle Sıvı Silikon Sızdırma veya kısaca LSI işlemi olarak adlandırılır .
Bu işlemlerde, artık gözeneklilik% 3'ten daha azdır.
Sinterleme ile matris üretimi
Oksit kompozit seramiklerde, matris malzemesi şu anda yüksek sıcaklıkta işlemle ("sinterleme") birincil malzemelerden üretilmektedir. Bu hammaddeler, sıcaklıkları , yaklaşık 1600 ° C olan geleneksel seramiklerin normal sinterleme sıcaklıklarından daha düşük tutmayı mümkün kılar . Mevcut oksidik lifler, bu kadar yüksek sıcaklıklarda çok fazla zarar görecektir. Birincil malzemeler, sözde bir kayma oluşturmak için az ya da çok yüksek oranlarda oksidik seramik tozları ile karıştırılan ve daha sonra elyaflara sokulan sıvılardır. 1000 ve 1200 ° C arasındaki sıcaklıklarda, oksit-seramik, gözenekli matris oluşturulur (güçlü hacim büzülmesiyle bağlantılı olarak). Malzemelerin bir örneği, Al karışımlarıdır 2 O 3 , tetra-etil-orto ile bir toz silikat doğru karışım içinde, (bir silikon ve oksijen verici olarak) ve (alüminyum vericisi olarak) alüminyum bütilat müllit bir matris olarak üretmek . Sol-jel yaklaşımları , sıvılar için başka olasılıklar olarak da belirtilmelidir. Bununla birlikte, tekniğin bilinen durumu, nanometre tanecik boyutlarına sahip tamamen sulu toz süspansiyonlarıdır ; burada farklı kalitede daha iri oksit-seramik tozları (alüminyum oksit, zirkonyum oksit) eklenir.
Burada ticari olarak kullanılan malzemenin gözenekliliği% 20 civarındadır.
Elektroforez ile matris üretimi
İçinde elektroforez , dağılmış elektriksel bir sıvı içinde parçacıkların olan yüklü, zıt yüklü bir yüzeye taşınan ve orada yatırılır iki elektrikli doğrudan voltajlı alanda elektrot . Yüzey olarak bir fiber yapı kullanılırsa, toz partikülleri burada birikir ve ayrıca fiberler arasındaki boşlukları doldurur. Bu şekilde üretilen elyaf takviyeli seramikler şu anda endüstriyel kullanımda değildir. Problemler arasında, tozun nispeten karmaşık hazırlanması ve dispersiyonu, yükün ayarlanması ve çok ince bileşen duvar kalınlıklarının sınırlandırılması yer alır.
Kalıcı gözeneklilik de burada erişim kanallarının aşırı büyümesiyle yaratılır.
özellikleri
Mekanik özellikler
Mekanik özelliklerin temel mekanizması
Girişte bahsedilen seramik liflerin seramik matriks içine gömülmesiyle bahsedilen çatlama direncindeki artış, aşağıdaki temel mekanizmaya dayanmaktadır:
Matris malzemesi yüklendiğinde, takviyesiz formdaki gibi% 0,05 gerildiğinde (matris tipine bağlı olarak) çatlaklar oluşturur ve gömülü lifler çatlak üzerinde bir köprü oluşturur. Bu köprüleme mekanizması, matrisin lifler boyunca kayabilmesini, yani liflere sadece mekanik olarak zayıf bir şekilde bağlanmasını gerektirir. Matris ve lifler arasında sıkı bir bağlantı ile, köprüdeki liflerin son derece yüksek uzayabilirliğe veya buna karşılık olarak düşük sertliğe sahip olması gerekir, ancak durum böyle değildir. Bu, sağlam bir bağlantı ile matris çatlağının da aynı noktada liflerden geçeceği ve fiber takviyeli seramiğin, güçlendirilmemiş seramiğin kırılgan kırılma davranışını gösterdiği anlamına gelir.
Bu nedenle , yüksek çatlama direncine sahip elyaf takviyeli seramiklerin sırrı, imalat sırasında elyaflar ve matris arasındaki bağlantının kaymaya izin vermesini sağlamaktır. Ancak bu şekilde, lifler çatlaklar üzerinde önemli bir köprü oluşturabilir ve uzayabilirliklerini ortaya çıkarabilir (C ve SiC lifleri için% 2'den fazla, Al 2 O 3 lifleri için neredeyse% 1). Elyaf takviyeli seramiklerin imalatında, bu kayma mekanizması genellikle elyafların karbon veya bor nitrür ile ince bir şekilde kaplanmasıyla sağlanır. Bu kaplamalar atomik olarak düzenlenmiş, lamel benzeri kayan düzlemlere sahiptir ve lifler ile matris arasında yağlayıcıyı oluşturur.
Oksit kompozit seramiklerin özel bir özelliği vardır: zayıf bağlantı, matrisin yüksek gözenekliliği veya fiber ile matris arasında yapay olarak oluşturulan boşluklar tarafından oluşturulur. İkincisi, örneğin, son sinterleme işlemi sırasında yanan ve karşılık gelen bir boşluk bırakan, örneğin karbon ile elyaflar üzerinde herhangi bir kaplama ile elde edilebilir. Bununla birlikte, çok yüksek bir matris gözenekliliği, düşük sıkıştırma ve eğilme mukavemetlerine yol açar, bu nedenle pratikte iyi mukavemet değerleri ile iyi kırılma davranışı arasında bir uzlaşma bulunması gerekir.
Çekme ve eğilme yükleri için özellikler, çatlama direnci
Fiber kaplamanın bu tür kompozit seramiklerin özellikleri üzerindeki etkisi , malzeme numuneleri üzerindeki eğilme mukavemeti , gerilme mukavemeti ve çatlama direncinin belirlenmesinde görünür hale gelir .

Başlık: SiSiC: geleneksel SiSiC , SiCSiC (CVI) ve CSiC (CVI): SiC / SiC veya C / SiC, CSiC (95) ve CSiC (93): LPI Sürecinde üretilen C / SiC, Ox (PP): oksit kompozit seramikler, CSiC (Si): LSI işleminde üretilen C / SiC.
Çentikli numuneler üzerindeki çatlak direnci ölçümlerinin eğrileri, sağdaki resimde örnek olarak gösterilmiştir. Bu testlerde, artan kuvvetle, çentikli bir numune (resme bakın) kırılıncaya kadar yüklenir. Kuvvet uygulayan zımbanın kuvveti ve yolu ölçülür. Olarak kırılma mekaniğinin , güç olan normalize için gerilme şiddeti faktörü (K olarak teknolojide bilinen SIF, 1c dikkate elde edilen kırılma yüzeyinin boyutunu alarak faktörü). Kompozit seramiklerde kırılma yüzeyinin boyutunun belirlenemediği ortaya çıktığı için, gösterilen eğriler yalnızca ilk çentiğin boyutuna göre normalleştirilir ve bu nedenle şekilde de biçimsel SIF "K" olarak anılır . Bu değer bir kuvvete karşılık geldiğinden , eğrilerin birbirleriyle göreli karşılaştırmasında eğrilerin altındaki alan ( integral ), numuneyi yok etmek için harcanması gereken enerji olarak kabul edilebilir. Sonuçlar, yalnızca numune geometrisi tüm numuneler için aynıysa doğrudan karşılaştırılabilir.
Resimde gösterilen farklı kompozit seramiklerin çatlak direnci eğrileri, kompozit seramik numuneler boyunca bir çatlağın sürülebildiği spesifik enerji harcamasının, geleneksel SiSiC seramiklerinin birçok katı olduğunu göstermektedir. Çeşitli çatlak direnci eğrilerinin maksimumları, çatlağın numuneden geçmesi için gereken kuvvet seviyesini gösterir. Farklı tipler ve üretim süreçleri, bu malzeme sınıfının niteliklerinde, özellikle çatlak direnci açısından fark edilebilir ve açık farklılıklara yol açar.
Malzeme Türü | Al 2 O 3 / Al 2 O 3 | Al 2 O 3 | CVI-C / SiC | LPI-C / SiC | LSI-C / SiC | SSiC |
---|---|---|---|---|---|---|
Gözeneklilik (%) | 25'i | <1 | 12'si | 12'si | 3 | <1 |
Yoğunluk (g / cm³) | 2.8 | 3.9 | 2.1 | 1.9 | 1.9 | 3.1 |
Çekme dayanımı (MPa) | 170 | 250 | 310 | 250 | 190 | 200 |
Kopmada uzama (%) | 0.3 | 0.1 | 0.75 | 0.5 | 0.35 | 0.05 |
Esneklik modülü (GPa) | 100 | 400 | 95 | 65 | 60 | 395 |
Eğilme dayanımı (MPa) | 350 | 450 | 475 | 500 | 300 | 400 |
Tablonun açıklamaları: CVI-, LPI- ve LSI- ön eki, ilgili C / SiC kompozit seramiğin üretim sürecini ifade eder. Kompozit seramikler için veriler ( Kaynak : W. Krenkel, s. 143), Pritzkow Spezialkeramik'ten oksit kompozit seramikler Al 2 O 3 için olanlardan ve HCStarck Ceramics'in bir veri sayfasından SSiC için verilerden gelmektedir. Ssic ve Al için gerilme mukavemeti 2 O 3 edildi hesaplanan gelen kopmada uzama ve elastiklik modülü bu yana, çekme dayanımları olan belirtilmemiş geleneksel seramik , ama genellikle sadece eğilme mukavemeti değerleri . Bunların ortalama değerler olduğu unutulmamalıdır. Geleneksel seramikler de dahil olmak üzere bireysel üretim süreçlerinde bazen belirtilen değerlerden önemli sapmalar olabilir.
Kompozit seramiklerin gerilme mukavemetini test ederken, geleneksel seramiklerin aksine, yarı plastik eğriler ve yüzde bire varan olası uzamalar, tüm teknik seramiklerin elastikiyetinin on katından fazla, çatlak köprüleme mekanizmasından kaynaklanır ; yarı-plastik çünkü doğrusal-elastik aralıktan sonra dönen eğri , malzemenin plastik deformasyonuna dayanmamaktadır , ancak lifler tarafından bir arada tutulan bir çatlak sisteminin oluşumundan kaynaklanmaktadır. Yük taşıyan lifler daha küçük bir esneklik modülüne sahip olduklarından, eğrinin eğimi azalır ve böylece plastik davranışı simüle eder. Burada da tablodaki değerler, farklı kompozit seramik türlerinin farklı derecelerde lif uzayabilirliğini kullandığını göstermektedir.
Eğilme mukavemetini belirlemek için ölçüm eğrileri, çatlak direncini belirlemek için yukarıda gösterilen eğrilerle pratik olarak aynı görünür. Çekme ve eğilme mukavemetlerini değerlendirirken, iki şey arasında bir ayrım yapılmalıdır:
- Çok az veya en uç durumda matris içermeyen malzeme yüksek gerilme mukavemetine (yani lif gerilme mukavemetine) sahiptir, ancak eğilme mukavemeti hemen hemen hiç yoktur.
- Tersine, yüksek matris içeriğine ve düşük gözenekliliğe sahip malzeme, yüksek eğilme mukavemetleri gösterir (geleneksel seramikler gibi), bu da liflerin esnekliğinin kullanılıp kullanılmadığı hakkında hiçbir şey söylemez.
Her iki değer de birbirinden bağımsız olarak görülmelidir.
Diğer mekanik özellikler
Kompozit seramikten yapılan birçok bileşende, lifler, istiflenmiş kumaş katmanları veya tek boyutlu olarak hizalanmış liflerin çapraz katmanları olarak iki boyutlu formdadır. Malzemeler bu nedenle anizotropiktir . Bu katmanlar arasında çatlakların yayılması herhangi bir fiber köprü tarafından engellenmez. Kumaşa dik gerilme mukavemeti gibi, laminat arası kayma mukavemeti değerleri de bu malzeme için uygun şekilde düşüktür . Elyaf takviyeli plastikte olduğu gibi, olası delaminasyon malzemede zayıf bir noktadır. Üç boyutlu fiber yapıların eklenmesiyle önemli ölçüde geliştirilebilir.
malzeme | CVI-C / SiC | LPI-C / SiC | LSI-C / SiC | CVI-SiC / SiC |
---|---|---|---|---|
Interlaminar Kesme Dayanımı (MPa) | 45 | 30'u | 33 | 50 |
Lif düzlemine dik çekme mukavemeti (MPa) | 6 | 4. | - | 7'si |
Elyaf düzlemine dik olan basınç dayanımı (MPa) | 500 | 450 | - | 500 |
Tablodaki yorumlar: Gözeneklilik nedeniyle, basınç dayanımı değerleri, silikon karbür için 2000 MPa'dan fazla belirtilen geleneksel seramiklere göre daha düşüktür. Gözeneklilik ve fiber köprülerin olmaması, fiber düzlemine dik olan çok düşük gerilme mukavemetlerine yol açar.
Liflerin çatlak köprüleme etkisi, bu seramiğin yüksek dinamik yüklere maruz kalmasına da izin verir. Örnekler, "düşük" veya "yüksek döngü yorgunluk" denilen alternatif yük testlerinde kırılıncaya kadar döngüsel basınca ve çekme yüklerine tabi tutulur. Başlangıç yükü ne kadar yüksek olursa, numune o kadar az döngüde kalır. Elde edilen döngü sayısının logaritmasına karşı çizilen farklı başlangıç yükleri, sözde Wöhler çizgisiyle sonuçlanır. Test edilen malzemenin belirli bir dinamik yük altında kaç bin veya milyonlarca yük döngüsüne dayanabileceğini gösterir. Fiberle güçlendirilmiş seramikler burada mükemmel sonuçlara ulaşabilir: Sünekliğin% 80'inde, döngüsel yüklere maruz kaldığında SiC / SiC, yaklaşık 8 milyon gerilim-sıkıştırma döngüsünde hayatta kalır (resme bakın).
Poisson oranı , ölçüm sırasında iki boyutlu elyaf düzlemine anormal bir durum dikey gösterir: bu, eğer bağlı tabakalar arası çatlak oluşumu, ilk fazda örnek kalınlığı artar kısaca liflerin dik doğrultuda negatif değerler alır yerine ölçümün azaltılması.
Termal ve elektriksel özellikler
Lif takviyeli seramiklerin ısıl ve elektriksel özellikleri, liflerin, matrisin ve gözeneklerin bileşenlerinden ve bunların bileşiminden kaynaklanmaktadır. Elyaf oryantasyonu ayrıca yöne bağlı ( anizotropik ) parametreler üretir .
Şu anda mevcut olan en yaygın kompozit seramikler şu şekilde özetlenebilir:
Oksitleri kullanan elyaf takviyeli seramikler hala çok iyi elektrik yalıtkanlarıdır ve gözenekler nedeniyle ısı yalıtım etkisi, geleneksel oksit seramiklere göre önemli ölçüde daha yüksektir .
Karbon fiberlerin kullanılması, onlarla doğrudan elektrik teması olur olmaz, fiberlerin yönündeki elektriksel ve termal iletkenliği arttırır.
Bir matris olarak silisyum karbür çok iyi bir ısı iletkenidir . Bir elektriksel yarı iletken olarak , elektrik direnci artan sıcaklıkla azalır . Amorf mikro yapıları nedeniyle silisyum karbür lifler, ısıyı ve elektrik akımını çok daha zayıf iletir. Matris olarak silisyum karbür içeren kompozit seramiklerde, gözeneklilik nedeniyle hem ısıl hem de elektriksel iletkenlik daha düşük değerlere düşmektedir. Bazı bilgiler aşağıdaki tabloda listelenmiştir.
malzeme | CVI-C / SiC | LPI-C / SiC | LSI-C / SiC | CVI-SiC / SiC | SSiC |
---|---|---|---|---|---|
Isı iletimi (p) [W / (m · K)] | 15 | 11 | 21 | 18'i | > 100 |
Termal iletkenlik (ler) [W / (m · K)] | 7'si | 5 | 15 | 10 | > 100 |
Termal genleşme (p) [10 −6 · 1 / K] | 1.3 | 1.2 | 0 | 2.3 | 4. |
Termal genleşme (ler) [10 −6 · 1 / K] | 3 | 4. | 3 | 3 | 4. |
belirli elektr. Direnç (p) [Ω · cm] | - | - | - | - | 50 |
belirli elektr. Direnç (ler) [Ω · cm] | 0.4 | - | - | 5 | 50 |
Tablo ile ilgili notlar: ile (p) ve (s) özelliklerdir s arallel ve s izotropik olmayan bir malzemeden enkrecht elyaf yönlendirmesine anlamına geliyordu. Girilmeyen değerlerle ilgili literatür veya üretici bilgisi yoktur. Düşük gözenekliliği nedeniyle, LSI malzemesi tüm kompozit seramikler arasında en yüksek termal iletkenliğe sahiptir - bu malzemeyi yüksek gerilimli fren diski malzemesi olarak kullanmak için bir avantaj. Burada da değerler, üretim sürecinin detaylarına bağlı olarak ayrı seramik türleri içinde bile önemli ölçüde değişebilir.
Normal seramikler ve teknik seramikler , termal şok yüklerine maruz kaldıklarında özellikle yüksek olan termal voltajlara duyarlıdır . Nedeni , bu malzemelerin düşük elastikiyetinde ve yüksek sertliğinde (yüksek elastiklik modülü ) yatmaktadır . Malzemedeki sıcaklık farklılıkları, yüksek elastikiyet modülü nedeniyle buna karşılık gelen yüksek gerilimlere yol açan farklı genişlemeler üretir. Bu, malzemenin aşırı gerilmesine ve kırılmasına neden olur. Lif takviyeli seramiklerde bu tür çatlaklar liflerle kapatılır. Seramik matriste çatlaklar oluşsa bile bir bileşen herhangi bir makroskopik hasara uğramaz. Bu malzeme sınıfının disk frenlerde kullanılması, kompozit seramiklerin aşırı termal şok koşullarındaki performansını kanıtlamaktadır.
Korozyon özellikleri
Elyaf takviyeli seramiklerin korozyon davranışına ilişkin daha kapsamlı çalışmalar henüz mevcut değildir. Burada da özellikler, kullanılan bileşenlerin özellikleri, yani elyaflar ve matris tarafından belirlenir.
Genel olarak, seramik malzemeler diğer birçok malzemeye kıyasla korozyona karşı çok dayanıklıdır. Farklı katkı maddelerine sahip çok sayıda üretim varyantı, örneğin sinterleme yardımcıları , karışık formlar, özellikle oksitlerle, safsızlıklar, tane sınırlarında cam fazları ve gözeneklilikteki farklılıklar , korozyon davranışı üzerinde belirleyici bir etkiye sahiptir ( Kaynak : J. Kriegesmann ).
Şu anda uygulamalarda önemli olan matris ve fiber malzemeler hakkında literatürden kısaca aşağıdakiler görülebilir:
- Alüminyum oksit: Çok saf haliyle,
alüminyum oksit hemen hemen her şeye dayanıklıdır; Tane sınırları ve silikon oksit içeriğindeki amorf cam fazlar, konsantre asitler ve alkalilerdeki korozyon oranını belirler . Yüksek sıcaklıklarda yük altında sürünme davranışına neden olurlar . Metal eriyikleri için, alüminyum oksit yalnızca altın veya platin gibi değerli metaller için kullanılır. - Alümina lifleri:
alüminaya benzer şekilde davranır. Ticari olarak temin edilebilen lifler aşırı saflıkta değildir ve bu nedenle daha kırılgandır. Yaklaşık 1000 ° C'nin üzerindeki sıcaklıklarda sürünme davranışı şu anda yalnızca birkaç oksit kompozit seramik uygulamasına izin vermektedir.
- Karbon:
Karbon , yaklaşık 500 ° C'lik sıcaklıklarda oksijenle korozyona uğrar, daha iyi yanar. Aynı zamanda güçlü oksitleyici ortamda (örneğin konsantre nitrik asit ) oksitlenir . Çoğu erimiş metalde karbürleri çözer veya oluşturur .
- Karbon lifleri:
Karbon lifleri pratikte karbon gibi davranır.
- Silisyum karbür:
Çok saf silisyum karbür çeşitleri, korozyona en dayanıklı malzemeler arasındadır. Sadece güçlü alkaliler, yaklaşık 800 ° C'den itibaren oksijen ve çoğu metal eriyiği bu malzeme ile reaksiyona girer. Erimiş metallerde hem karbürler hem de silisitler (metalli silikon bileşikleri) oluşur.
SiC, SiO 2 ve CO 2 oluşturmak için oksijenle reaksiyona girdiğinde , silikon dioksit pasifleştirici bir etkiye ("pasif oksidasyon") sahip koruyucu bir tabaka oluşturur. Daha da yüksek sıcaklıklarda (yaklaşık 1600 ° C'den itibaren) ve aynı anda oksijen eksikliğinde ( 50 mbar'ın altındaki kısmi basınç ), bununla birlikte, CO 2 ve CO'ya ek olarak , herhangi bir koruyucu etkiyi önleyen gaz halindeki silikon monoksit (SiO) oluşur. Bu sözde "aktif oksidasyon", bahsedilen koşullar altında silisyum karbürün çok hızlı bozulmasına yol açar.
Kompozit seramiklerle bağlantılı olarak, bu karakterizasyon yalnızca CVI işlemi kullanılarak üretilmiş SiC matris malzemesi için geçerlidir. Orada matris çok saf, ince kristal SiC'den oluşur. LPI prosesi ile üretilen matris, amorf yapısı ve gözenekliliği nedeniyle her türlü korozyona karşı önemli ölçüde daha hassastır. LSI malzemesinin matrisinde her zaman bulunan silikon kalıntıları, bozulmuş bir korozyon direncine neden olur. - Silisyum karbür lifler:
Silisyum karbür lifler, çapraz bağlı organosilikon sentetik reçinelerin (karbon liflerinin üretimine benzer) pirolizi ile üretildiğinden, aynısı LPI işleminde üretilen matris için de geçerlidir: korozyona karşı önemli ölçüde daha fazla hassasiyet alkaliler ve oksitleyici ortam ile.
Başvurular
Elyaf takviyeli seramiklerle, artık geleneksel teknik seramiklerin önemli dezavantajlarına, yani düşük kırılma tokluğuna ve yüksek termal şok hassasiyetine sahip olmayan bir malzeme mevcuttur. Uygulama geliştirmeleri sonuç olarak, artık metaller tarafından erişilemeyen yüksek sıcaklıklarda ve aşındırıcı (= aşınmaya neden olan) yükler altında güvenilirliğin gerekli olduğu alanlar üzerinde yoğunlaşmıştır . Şimdiye kadarki gelişmeler ve uygulamalarda aşağıdaki öncelikler ortaya çıkmıştır:
- Dünya atmosferine yeniden girdiklerinde yüksek termal voltajlara ve titreşimlere maruz kalan uzay araçları için ısı koruma sistemleri .
- Sıcak gazlar alanındaki gaz türbinleri için bileşenler , yani türbin yanma odası , gaz akışını yönlendiren statik kılavuz kanatları ve gaz türbininin kompresörünü çalıştıran gerçek türbin kanatları .
- Brülör teknolojisi için bileşenler ve oksit kompozit seramikten yapılmış sıcak gaz kanalları.
- Sürtünme yüzeyinde aşırı termal şok koşullarına maruz kalan ağır yüklü disk frenler için fren diskleri (parlayan bir parçanın suya daldırılmasından farklı olarak, burada ısı yalıtıcı su buharı tabakası yoktur).
- Yüksek korozyon ve aşınma yüklerine sahip kaymalı yataklar için bileşenler .
Ek olarak, geleneksel teknik seramiklerin kullanıldığı veya metalik bileşenlerin korozyon veya yüksek sıcaklıklar nedeniyle tatmin edici bir hizmet ömrü sağlamadığı tüm alanlar ilgi çekicidir. Bazı geliştirme ve uygulama örneklerinin aşağıdaki sunumu tam olmaktan uzaktır ve yalnızca teknik olasılıkların genişliğini göstermeyi amaçlamaktadır.
Uzay uygulamaları için gelişmeler
Havacılık sektöründe , fiber takviyeli seramikler, ısı koruma sistemlerinin bileşenleri ve uzay planörlerinin hareketli kontrol kanatları için ilgi çekicidir . Dünya atmosferine yeniden girerken, bu elementlerde birkaç dakika için 1500 ° C'nin üzerinde yüzey sıcaklıkları ortaya çıkar ve bu, yalnızca seramik malzemelerle büyük bir bozulma olmaksızın dayanabilir. Uzay yolculuğunda sıcak yapılar için fiber takviyeli seramiklerin kullanımı, diğer şeylerin yanı sıra, daha önce kullanılan malzeme sistemlerinden farklı olarak vaat ediyor:
- Ağırlık tasarrufu
- Isı koruma sisteminin taşıyıcı yapıya katkısı
- Birden çok yeniden giriş için yeniden kullanılabilirlik
Mevcut oksit fiberler yana sürünme bu yüksek sıcaklıklarda yük altında ve amorf SiC-lifleri nedeniyle yeniden kristalizasyon için kendi gücünü kaybeder, malzeme ve bileşen gelişmeler bileşik seramik C / SiC üzerinde yoğunlaşmıştır. Parçası HERMES -Programmes ESA içinde 1980 yürütülen ve geliştirme ve burun konisi yeterlilik, kanat lider kenarları ve uzay uçağın kuyruk kontrolü kanatlı doruğa birkaç takip programlarıyla sonra 1992 kırık gelişmeler X-38 arasında NASA bulundu.
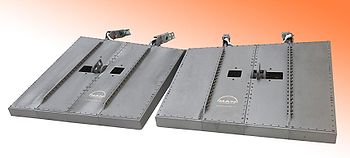
Boyut: 1.5 × 1.5 × 0.15 m, ağırlık: her biri 68 kg, her biri CVI-C / SiC'den yapılmış 400'den fazla vida / somun ile ayrı parçalardan birleştirilmiş.
Fotoğraf: MT Aerospace
Bu gelişmelerden biri, örneğin, kompozit seramiklerden yapılan vidaların ve somunların nitelendirilmesine hizmet etti. Teknik seramikten yapılmış vidalar mevcuttur, ancak diş kökündeki çentikler nedeniyle kırılgandırlar ve şu ana kadar gerekli güvenilirliğe sahip değildirler. C / C'den yapılan vidaların kullanımı da oksidasyona duyarlılığı nedeniyle çok risklidir.
Bu kontrol kanatlarının bir diğer önemli bileşeni, hareket için kuvvetin uygulandığı merkezi olarak yerleştirilmiş yataktır. Bu yatak başarılı oldu test gerçek koşullar altında (4 ton yük, alt 1600 ° C, dünyanın atmosferi ve dört saniye içinde bir hareket devri ile aynı anda 8 ° dayanma hareketleri yeniden giren düzeyde oksijen konsantrasyon) DLR olarak Stuttgart; bu şekilde beş yeniden giriş aşaması simüle edildi.
C / SiC kullanımı, yeniden giriş koşulları altında C elyaflarının hızlı yanmasını önleyen kaplama sistemlerinin geliştirilmesini ve kalifikasyonunu zorlamıştır. Simüle edilmiş yeniden giriş koşulları altında plazma akışındaki deneyler , bu geliştirme çalışmasının başarısını kanıtlamıştır.
Uçuşa elverişlilik için bir başka yeterlilik adımı , Münih'teki bir IABG test standında 1000 ° C'nin üzerinde deformasyon testleri ile gerçekleştirildi . 4 ton yük altındaki deformasyon, ilgili hesaplamaları ve tasarımı doğruladı. Uçuş testi için planlanan ABD, Teksas, Houston'daki X-38 uzay planörüne kanatların yerleştirilmesinden sonraki son yer testleri de başarılı oldu. Mali nedenlerden ötürü, NASA artık projenin amacına, yani X-38'in bir uzay mekiği uçuşuyla yörüngeye taşınması ve ardından (insansız) dünya atmosferine yeniden giriş hedefine ulaşamadı.
Bu noktada belirtilmelidir ki, bu nitelikler bu özel durum için C / SiC kompozit seramiklerin kullanımına hizmet etmektedir. Yüksek sıcaklık yükü yeniden girildiğinde yaklaşık 20 dakika sürer. Yeniden kullanılabilirse, süre birkaç saatlik döngüsel yüklemeye kadar eklenir. Yüzlerce veya binlerce saatlik hizmet ömrü ile endüstriyel yüksek sıcaklık uygulamaları için oksidasyon korumalı C / SiC kullanımı henüz garanti edilmemiştir.
Gaz türbinlerinde kullanıma yönelik gelişmeler
Gaz türbinlerinde kompozit seramik kullanımının amacı, gaz sıcaklığının artırılması, bu da verimin artmasına neden olmaktır.
Gaz türbinlerindeki kılavuz kanatların ve türbin kanatlarının karmaşık şekli ve bu parçalar üzerindeki çok yüksek termal ve mekanik stres, başlangıçta yalnızca kompozit seramikten yapılmış yanma odalarının geliştirilmesinin başarılı bir şekilde desteklenmesine yol açmıştır . Amerika Birleşik Devletleri'nde bu alanda ilerleme en ileri seviyeye ulaştı. Yüksek sıcaklığa dayanıklı özel bir SiC elyafı bazlı SiC / SiC kompozit seramikten yapılmış bir yanma odası, bir gaz türbininde 15.000 saatin üzerinde kullanılmaktadır. SiC, bu tür dönemlerde 1100 ° C civarındaki sıcaklıklarda oksidasyon tarafından gözle görülür şekilde saldırıya uğradığından, burada da çok etkili bir oksidasyon korumasının geliştirilmesi gerekiyordu. Çok katmanlı bir oksit seramik sisteminden oluşur.
Test edilen sıcaklık seviyesinin, hava filmi ile soğutulan geleneksel metalik yanma odalarına kıyasla henüz herhangi bir avantaj sunmaması ve yanma odasını takip eden bileşenlerin (kılavuz kanatlar ve türbin kanatları) da daha yüksek bir sıcaklık seviyesi için geliştirilmiş ve geliştirilmiş olması , gerçek uygulamalarda şimdiye kadar elde edilen sonuçların hızlı bir şekilde uygulanmasını engelleyen nitelikli olması ve kompozit malzeme sisteminin özel SiC fiberlerden, SiC matrisinden ve özel kaplama sisteminden üretim maliyetleri hala çok yüksek.
Brülörlerde ve sıcak gaz kanallarında oksit kompozit seramik kullanımı
Oksijen içeren, 1000 ° C'den yüksek sıcaklığa sahip sıcak gazlar , silikon karbürden yapılmış tüplerin oksidasyonla zarar görmesi durumunda, ölçeklenmelerine yüksek sıcaklığa dayanıklı çelikten yapılmış geleneksel alev tüplerine sahip brülörlerde er ya da geç kurşun . Bu parçalar yüksek mekanik gerilime değil, sadece güçlü termal şoklara maruz kaldıklarından, oksit kompozit seramikler özellikle 1300 ° C'ye kadar olan bu tür uygulamalar için uygundur. Aşağıda yer alan görüntüler için bir pişirme doğrultusunda 15.000 saat kullanılmış olan oksitli alüminyum oksit kompozit seramik bir ocak, bir alev borusu dizi Gevrek ve şimdi 20.000'den fazla çalışma saatleri ulaşmıştır. Bu uygulamalarda geleneksel malzemelere göre 20 katına kadar hizmet ömrü elde edilebilir.
Çeşitli sistemlerde oksijen içeren sıcak gaz akışlarını düzenlemek veya taşımak için kanatlar veya fanlar, metallerle aynı formda oksit kompozit seramiklerden yapılabilir. 650 ° C'nin üzerindeki sıcaklıklarda metaller gibi deforme olmama (" bükülme ") avantajına sahiptirler. Bu malzemenin kapıları kaldırmak için kullanılması (bkz. Resim serisi), örneğin sık sık açma ve kapama işlemleriyle 1300 ° C'ye kadar yüksek termal yüklere de maruz kalan sinterleme fırınlarında, bir defada kendini kanıtlamıştır. 260.000'den fazla açma ve kapama döngüsüyle 12 ay.
Fren diski olarak kullanın
Göre fren diskleri uzun olmuştur / C malzemeden imal yarış arabası arasında formül 1 kullanılır ve uçakların frenlerde, hemen fren diskleri arasında yapmış C / SiC LSI işlemle hazırlanır malzeme, ticari olarak temin edilebilir ve pahalı spor arabalara monte edilir, bazen ek bir maliyetle. LSI süreci, üretimde maliyet avantajları sunar. Kısa elyaf ve reçine karışımından yapılan bölmeler preslenir, sertleştirilir, bir C / C bölmesi oluşturmak için pirolize edilir ve daha sonra, yukarıda tarif edildiği gibi, nispeten hızlı ve ucuz bir şekilde erimiş silikonlu bir LSI-C / SiC bölmesine dönüştürülür.
Bu fren disklerinin avantajları şu şekilde özetlenebilir:
- Disk aşınması çok düşük. Geleneksel bir gri dökme demir rondelaya kıyasla hizmet ömrü yaklaşık altı kat daha uzundur. Sürüş tarzına bağlı olarak, bu aynı zamanda aracın tüm hizmet ömrü boyunca bir pencere kullanımına izin verir. Normal yük altında 300.000 km'ye kadar belirtilmiştir.
- Yüksek gerilim altında bile , metal disklerden bilinen sözde solma etkisi olan sürtünme katsayısında herhangi bir dalgalanma yoktur .
- C / C'den yapılan fren disklerinin aksine, nemin fren performansı üzerinde hiçbir etkisi gözlenmez.
- Cam malzemesi aşınmaya son derece dayanıklıdır ve bu nedenle kışın yol tuzunun etkilerine karşı duyarsızdır.
- Kütle, çelik diske göre yaklaşık% 40 azaltılabilir. Tekerleklerin önemli ölçüde daha düşük yaylanmamış kütlesi nedeniyle, bu, daha iyi sürüş konforu ve aynı zamanda daha iyi yol tutuşu anlamına gelir, çünkü tekerlek zeminin dış hatlarını daha kolay takip edebilir.
C lifleri SiC matrisi tarafından oksidasyondan büyük ölçüde korunduğundan ve fren disklerinin 500 ° C'nin üzerindeki sıcaklıkları önemli ölçüde aşabildiği süre, bir aracın tüm hizmet ömrü boyunca birkaç saat ile sınırlandırıldığından, malzemenin oksidasyonu söz konusudur. Bu Uygulamadaki bir rol önemli değil.
Bu tür pencerelerin imalat maliyetlerinin, orta sınıf araçların da bunlarla donatılabilecek kadar düşürülebileceğini görmek gerekiyor. Mevcut durum, sağlayıcıların web sitelerinde bulunabilir.
Kaymalı yataklardaki uygulamalar
Konvansiyonel SSiC veya daha az pahalı Sisic büyük bir başarı ile kullanılmaktadır içinde kaymalı yataklar üzerinde 20 yıldır pompalar için ( Lit :. WJ Bartz, 2003). Yatak, pompanın sağladığı sıvıyı yağlayıcı olarak kullanır . Bu rulman konseptinin başarısının nedeni, hemen hemen tüm ortamlara karşı korozyon direnci ve sürtünme yükleri veya partiküllerden kaynaklanan aşındırıcı yükler altında büyük sertlik ve ayrıca sıvı yağlama ile düşük sürtünme katsayısının neden olduğu son derece düşük aşınmadır . Kaymalı yatağın SiC bileşenleri, şafta monte edilen ve yatak burcu içinde dönen şaft koruma manşonundan oluşur. SiC yatak burcu genellikle metalik ortamına çekilir ve sıkıştırma gerilimi altındadır . Bu nedenle, bu bileşenin gevrek kırılması pek olası değildir. SiC şaft koruma manşonu bu avantaja sahip değildir ve bu nedenle genellikle büyük bir duvar kalınlığında tasarlanır ve / veya özel yapısal önlemler alınarak monte edilir. Uygun şekilde büyük şaft çaplarına (100 ila 300 mm) sahip büyük pompalarda ve yüksek yatak yüklerine sahip pompalarda, seramik yatak konsepti, koruyucu şaft kovanının arızalanma riski nedeniyle yalnızca kompozit seramiklerin kullanılmasıyla uygulanabilir. Test tezgahında, CVI-SiC / SiC ve geleneksel SSiC'nin rulman çiftinin, test edilen diğer birçok çiftin olduğu gibi karışık sürtünme koşulları altında spesifik rulman yükünün neredeyse üç katına dayanabildiği gösterilebilir . İle belirli bir yüke sürtünme (boyutsuz), çalışma hızı (m / s) ve yatak yük (MPa veya N / mm²'lik) kastedilmektedir katsayısı ürünüdür; yatak boşluğunda dönüştürülen gücü W / mm² cinsinden gösterir ve genellikle sürtünme katsayısını çıkararak "P çarpı V değeri" olarak verilir.
Kazan besleme suyu pompaları olarak enerji santralleri olan sıcak su ile birkaç bin m³ / h, 160 ° C 20 bar basınçta pompalanır, ya da tüp şeklindeki kılıf, pompalar birkaç olan on şurada kilit su veya deniz suyunun bin m³ / h tuz giderme tesisler pompalanır, 1994 yılından beri tuzdan arındırma tesisleri için tercih edilen uygulamalar olmuştur, CVI-SiC / SiC kompozit seramikten yapılmış şaft koruyucu manşonlara sahip su yağlamalı kaymalı yataklar (bu makalenin başındaki resim).
Havacılık motorlarında sıvı oksijenin (Sıvı Oksijen = LOx, kaynama noktası: −183 ° C) iletildiği turbo pompalarda bu tip kaymalı yatak uygulaması hala geliştirme aşamasındadır . Şimdiye kadar yapılan testler şunları göstermiştir:
- SiC ve CVI-SiC / SiC, LOx ile uyumludur ve ağır koşullar altında bile oksijenle reaksiyona girmez (kendiliğinden tutuşma sıcaklığını belirlemek için toz, Fransız standardı NF'ye göre 20 bar saf oksijen gazı altında 525 ° C'ye kadar ısıtılır. 29-763.).
- Sürtünme aşınma testleri yarıya göstermiştir sürtünme katsayısı ve aşınma yüzüncü indirgenmiş standart metalik eşleştirme ile karşılaştırıldığında .
- Yağlama hidrostatik tasarımlı rulmanlara sahip LOx, farklı yatak yükleriyle 10.000 dak -1 hızda birkaç saatlik bir teste sahiptir ve karışık sürtünme koşulları altında 50 Başlatma / Durdurma alanı pratikte aşınmadan hayatta kalmıştır.
Kompozit seramikli bu seramik rulmanların, geleneksel seramikli rulmanlara kıyasla avantajı, büyük ölçüde artırılmış güvenilirliktir. Koruyucu şaft kovanının hasar görmesi, birkaç büyük ve sert parçaya bölünmesine ve pompa muhafazasında ve çarkta büyük dolaylı hasara yol açmaz.
Diğer uygulamalar ve geliştirme yaklaşımları
Aşağıdaki uygulama ve geliştirme örneklerinden de bahsedilebilir:
- İtki kontrol kanatlar jet motorlarının bir savaş uçağı hangi, püskürtme kesit motor gücüne uyarlanmıştır.
- Füzyon reaktörlerinin sıcak alanlarının astarı olarak üç boyutlu fiber yapıya sahip CVI-SiC / SiC plakaları . Üç boyutlu fiber yapı, plakanın düzlemine dik olarak ısı iletimini arttırır. Kristalin SiC'nin nötron radyasyonuna maruz kalan ortamda nispeten stabil bir malzeme olduğu kanıtlandığından, burada yüksek sıcaklık stabilitesi amorf ile karşılaştırıldığında büyük ölçüde geliştirilmiş olan kristalin SiC fiberleri de kullanılır.
- Süpersonik roketlerdeki iticiler ("kanatçıklar"), alev tutucular ve sıcak gaz yönlendirme boruları, katı yakıtlarda aşırı sıcak egzoz gazlarını kontrollü bir şekilde kısa bir süre için yine partiküllerle yönlendirmek ve saptırmak zorundadır.
- Otomobil trafiğindeki kazalar için simülasyon sistemlerinde kızakların hızlı frenlenmesi için fren balataları, düşük aşınma ve yıpranma avantajıyla ve hatta birkaç testle bile çok kararlı fren yavaşlama değerleri.
- Gaz türbinlerindekine benzer şekilde sıcak gaz korozyonu sorunları olan ve ayrıca gerekli gaz sızdırmazlığı olan yüksek sıcaklıklı ısı eşanjörleri .
- Hassas aynalar için sert yapılar.
- Formula 1 yarış arabalarının egzoz boruları alanındaki kaplama elemanları ve bu araçların ağır yüklü debriyajları için diskler .
Avrupa'daki endüstriyel üreticiler
- WPX fiber seramik: Endüstriyel ısıl işlem ve yüksek sıcaklık uygulamaları için oksidik fiber seramik parçalar ve bileşenler
- KLETKE Advanced Composites: C-CVI ve LSI süreçleri kullanılarak SiC kaplamalı C / C, C / C'den yapılmış bileşenler
- SGL Carbon : Fren diskleri (LSI süreci)
- Schunk Group : Eksenel rulmanlar, radyal rulmanlar, kaymalı astarlar, C / C malzemeden yapılmış fırın astarları
- BJS Ceramics: havacılık bileşenleri, kaymalı yatak bileşenleri (CVI süreci)
- Snecma : Uzay yolculuğu, savunma teknolojisi, fren diskleri (CVI süreci) için bileşenler
- Brembo : fren diskleri (LSI süreci)
- Pritzkow özel seramikleri: Endüstriyel ihtiyaçlar için oksit kompozit seramiklerden yapılmış yüksek sıcaklığa dayanıklı bileşenler
- CERAFIB GmbH: Yüksek sıcaklığa dayanıklı filamentler ve malzemeler
Almanya'daki araştırma kurumları
- Bremen Üniversitesi : Seramik Malzemeler ve Bileşenleri ve Biyoseramik Bölümü
- Stuttgart Üniversitesi : Seramik Bileşen Üretim Teknolojisi Enstitüsü (IFKB)
- Karlsruhe Üniversitesi : Makine Mühendisliğinde Seramik Enstitüsü (IKM)
- Dresden : Fraunhofer Seramik Teknolojileri ve Sistemleri Enstitüsü ( IKTS ) ve TU Dresden'deki Hafif Yapı ve Polimer Teknolojisi Enstitüsü (ILK)
- Bayreuth Üniversitesi : Malzeme Araştırma Enstitüsü'nde (IMA) Seramik Malzemeler Başkanı
- Tekstil Kimyası ve Suni Elyaf Enstitüsü (ITCF Denkendorf): elyaf araştırma ve geliştirme
- DLR Yapı ve Yapısal Teknoloji Enstitüsü: Özel yapım CMC malzemelerinin geliştirilmesi, ör. B. Termal koruma sistemleri
- Fraunhofer Center for High Temperature Lightweight Construction (HTL): Araştırma ve geliştirme Seramik Matris Kompozitleri (CMC), seramik elyaflar ve yüksek performanslı seramikler
Edebiyat
- W. Krenkel (Ed.): Seramik kompozit malzemeler . Wiley-VCH, Weinheim 2003. ISBN 3-527-30529-7
- J. Kriegesmann (Ed.): DKG - Teknik Seramik Malzemeler . HvB-Verlag, Ellerau 2005. ISBN 978-3-938595-00-8
- WJ Bartz (Ed.): Seramik rulmanlar, malzemeler - düz ve makaralı rulmanlar - contalar . Triboloji ve Yağlama Teknolojisi El Kitabı. Cilt 12. Uzman Verlag, Renningen 2003. ISBN 3-8169-2050-0
Referanslar
- ↑ Narottam P. Bansal, Jacques Lamon: Seramik Matris Kompozitler Malzemeler, Modelleme ve Teknoloji . John Wiley & Sons, 2014, ISBN 978-1-118-83289-9 , s. XV ( Google Kitap Arama’da sınırlı önizleme ).
- ↑ M. Kunz, "Ceramic Matrix Composites" , cfi / report of the DKG, Volume 49, No. 1, 1992, s.18
- ↑ M. Kunz: Seramik elyaf kompozitlerin çatlama direnci . Karlsruhe Üniversitesi'nde Tez, Shaker Verlag , Aachen, 1996.
- ↑ A. Mühlratzer, M. Leuchs: Non-Oxide CMCs Applications , from: High Temperature Ceramic Matrix Composites , Ed. W. Krenkel ve diğerleri, Wiley-VCH, Weinheim, 2001, ISBN 3-527-30320-0 , S. 288
- ^ H. Pfeiffer: X-38 ve CRV için Seramik Gövde Kapağı . 2. Uluslararası Atmosferik Yeniden Giriş Araçları ve Sistemleri Sempozyumu, Arcachon, Fransa, Mart 2001
- ^ H. Pfeiffer, K. Peetz: X-38'de Uzay Uçuşuna Uygun Tamamen Seramik Gövde Kapağı . 53rd International Astronautical Congress, Houston, Texas, USA, October 2002, Paper IAF-02-I.6.b.01
- ↑ H. Lange, M. Dogigli, M. Bickel: Yüksek Sıcaklık Uygulamaları için Seramik Bağlantı Elemanları . 5. Uluslararası Katılım Konferansı: Seramik, Glas ve Metal, Jena, Mayıs 1997, DVS raporları Cilt 184, Deutscher Verlag für Schweißtechnik, s. 55, ISBN 3-87155-489-8
- ↑ M. Dogigli, H. Weihs, K. Wildenrotter, H. Lange: Uzay Araçları için Yeni Yüksek Sıcaklık Seramik Rulman . 51.Uluslararası Astronotik Kongresi, Rio de Janeiro, Brezilya, Ekim 2000, Makale IAF-00-I.3.04
- ↑ N. Miriyala, J. Kimmel, J. Price, H. Eaton, G. Linsey, E. Sun: Bir gaz türbininde saha testinden sonra CFCC astarının değerlendirilmesi - III . ASME Turbo Expo Land, Sea & Air, Amsterdam, Haziran 2002, Kağıt GT-2002-30585
- ^ KL More, PF Tortorelli, LR Walker, JB Kimmel, N. Miriyala, JR Price, HE Eaton, EY Sun, GD Linsey: Motor ve Laboratuar Maruziyetlerinden Sonra Seramik Matris Kompozitlerde Çevresel Bariyer Kaplamalarının Değerlendirilmesi . ASME Turbo Expo Land, Sea & Air, Amsterdam, Haziran 2002, Paper GT-2002-30630
- ↑ WEC Pritzkow: En yüksek talepler için bir malzeme olan seramik levha . DKG-DGM Sempozyumu Yüksek Performanslı Seramikler için cfi özel baskısı 2005, W. Krenkel (Ed.), ISSN 0173-9913 , s.
- ↑ WEC Pritzkow: Oksit-Elyaf Takviyeli Seramikler . cfi / Ber. DKG 85 (2008) No. 12, sayfa E1
- ↑ a b K. Gaffal, A.-K. Usbeck, W. Prechtl: Yeni malzemeler, kazan sistemlerinde besleme suyunun pompalanması için yenilikçi pompa konseptleri sağlar . VDI raporları No. 1331, VDI-Verlag, Düsseldorf, 1997, s.275
- ↑ W. Kochanowski, P. Tillack: Yeni pompa yatak malzemeleri, boru şeklindeki gövdeli pompaların hasar görmesini önler . VDI raporları No. 1421, VDI-Verlag, Düsseldorf, 1998, s.227
- ↑ JL Bozet, M. Nelis, M. Leuchs, M. Bickel: Hidrostatik Yatak Tasarımı ile Bağlantılı SiC / SiC Seramik Matris Kompozitlerinin Sıvı Oksijenindeki Triboloji . 9. Avrupa Uzay Mekanizmaları ve Triboloji Sempozyumu Bildirileri (ESMAT), Liège, Belçika, Eylül 2001, ESA Document SP-480, s.35
- ↑ M. Bickel, M. Leuchs, H. Lange, M. Nelis, JL Bozet: Kriyojenik Turbo Pompalarda Seramik Makaralı Rulmanlar . 4. Uluslararası Başlatıcı Teknolojisi Konferansı - Space Launcher Liquid Propulsion, Liège, Belçika, Aralık 2002, Makale # 129
- ↑ P. Boullon, G. Habarou, PC Spriet, JL Lecordix, GC Ojard, GD Linsey, DT Feindel: Gaz Türbini Uygulamaları için Kendinden Sızdırmaz Seramik Matris Kompozitin Karakterizasyonu ve Nozul Test Deneyimi , ASME Turbo Expo Land, Sea & Air, Amsterdam, Haziran 2002, kağıt GT-2002-30458
- ^ B. Riccardi, L. Giancarli, A. Hasegawa, Y. Katoh, A. Kohyama, RH Jones, LL Snead: Füzyon Reaktörleri için SiC f / SiC Kompozit geliştirmedeki Sorunlar ve Gelişmeler . Journal of Nuclear Materials, Cilt 329-333, 2004, s.56
- ↑ bir b c d W. Krenkel: elyaf takviyeli C / C-SiC-seramiği uygulama potansiyelleri bölgesi Lit :.. W. Krenkel, 2003, s 220